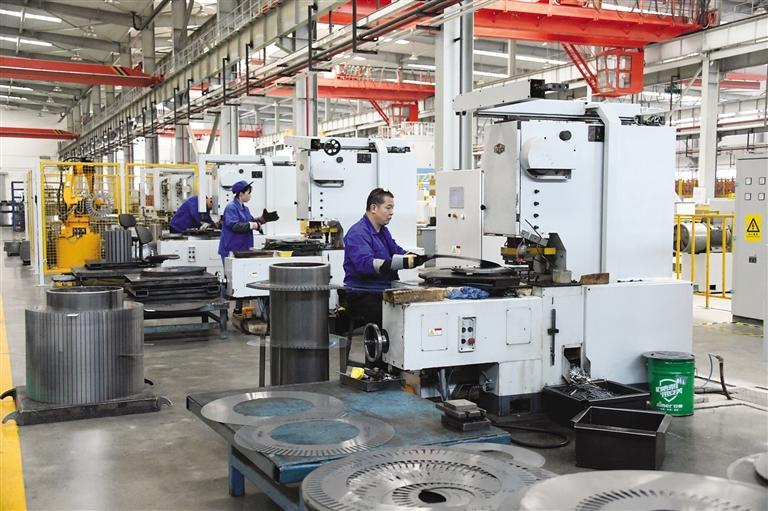
冲剪制造部生产现场 赵丽君 摄
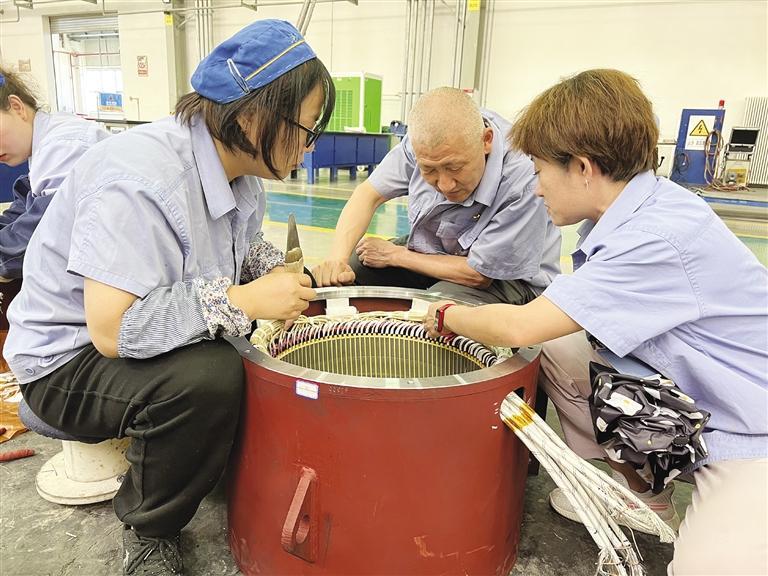
兰州电机杯青工技能大赛现场 受访企业供图
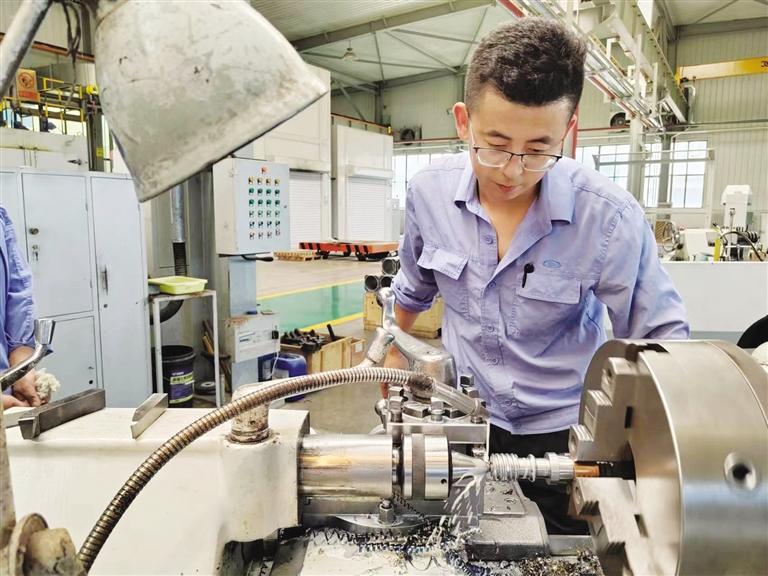
在比赛中提升技能 受访企业供图
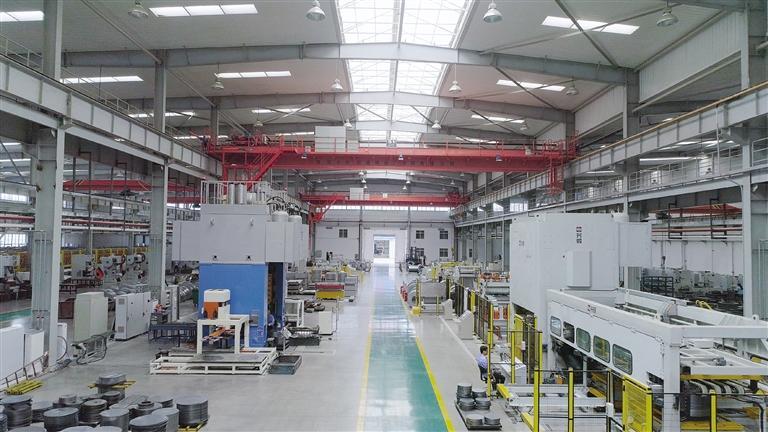
兰州电机冲剪制造部数字化车间 赵丽君 摄
中国甘肃网6月12日讯 据兰州晚报报道(记者 张丹)企业少闲月,六月人倍忙。走进兰州电机股份有限公司(以下简称“兰州电机”)冲剪制造部车间,电机轴类智能化加工生产线让人眼前一亮:机械手臂和智能设备高效运转,互联冲压机器人工作站的机器人在有序抓料、冲压、理片,每个程序耗时不过几秒钟;工人分工合作,把各式各样的零部件组装成电机总成产品。
“目前,我们已拥有加工、检测及试验设备1600余台套,主要设备数控化率达86%以上,先进的数控加工中心,冲剪、焊接、线圈制造、浸漆、检测等电机制造关键工序实现了数字化、智能化,年综合生产能力1000万千瓦。”兰州电机科技管理部部长赵庆礼说,智能制造是保持企业旺盛生命力的关键所在,“只有聚焦关键环节,集中攻关,促进信息技术、智能化技术和绿色环保技术融入产品全生命周期管理,才能为企业大跨步发展提供有力支撑。”
智能制造
持续推进关键工序智能化改造升级
深耕电机制造业60余年,兰州电机主要从事大中型电机、中小型发电机、特种及伺服电机、新能源装备电机的研发制造和服务以及电机维修再制造产业,立足为客户提供电机系统的解决方案。从上世纪八九十年代引领电机行业技术发展潮流,到本世纪初接受市场化改革重组,再到如今成长为我省电机行业链主企业,其产品广泛应用于电力、水利、建材、冶金、矿山、石油化工、城市基础设施建设、武器装备等领域。
走进兰州电机生产车间,宽阔明亮的厂房内,一条条加工、装配生产线整齐排列。正在作业的生产线上,只有一两名工程师在控制屏幕上监控、调整数据参数,车间内只有金属零件碰撞和设备运行的声音。
这是兰州电机引进的国内第一条多品种、小批量、柔性化生产的中小型电机轴类智能化加工生产线。在这个电机轴类柔性生产单元,可实现从取料到加工再到检测的全序化生产。通过多年探索和创新,兰州电机多个工艺环节已实现自动化甚至无人化,包括智能控制VPI真空浸漆系统,实现了浸漆过程中的全数字化、自动控制,有效保证了电机的定转子绝缘,实现操作过程实时监测,使浸漆效率提高了30%;电机轴及风扇焊接机器人工作站的引进,使焊接质量有了大幅提升,尤其是焊缝的表观质量实现了质的飞跃,使铆焊事业部一次交检合格率在原有基础上提升了6%;冲剪制造部通过生产线改造及双机互联冲压机器人工作站的引进,实现了从抓料、冲压、到理片的全自动化生产,提高生产效率23%以上,人员减少40%等。记者在现场采访时发现,偌大的车间里没有多少人,许多工位是“两三人+自动化设备”的组合。“我们的多条生产线全部实现了数字化和自动化,达到国内领先及国际先进水平,成功获批甘肃省第一批省级数字化车间。”赵庆礼自豪地说。
在兰州电机,智能化的亮点不仅在制造环节。
在研发环节,利用计算机三维工程分析软件,进行电机设计仿真分析,对电机各种电磁方案进行计算、比较、分析、优化。过去,新开发产品在定型前,必须按照设计图实打实地生产一台样机,用以验证设计方案;而数字化后,新产品在完成设计的同时,会有一台结构、功能高度仿真的“数字样机”在电脑中同步诞生,供研发部门进行全方位验证,实现了电机三维设计与工艺仿真、信息采集与优化管理、生产计划与制造执行的完美结合,使兰州电机产品进入到全生命周期管理阶段,极大地缩短了产品的研发周期,保证研发过程中数据的可追溯性。
在检测环节,兰州电机以大中型电机试验系统建设为试点,中小型发电机、伺服电机试验站同步推进,融合信息化以试验站计算监控系统、试验数据采集分析系统以及试验数据管理系统为工具,完成试验设备的监视、控制、远程操作,实现电机数据的采集、存储分析、处理,实现电机从设计研发、生产制造、试验检测,到维修再制造的全生命周期管理。
绿色为底
为企业高质量发展注入更多韧性
“传统产业智能转型升级为企业开展科技创新和产品工艺路线优化,提供了数据支撑及设备保障,也体现了公司加快转型升级、绿色制造步伐的发展信心。”赵庆礼表示,随着研发、制造、检测设备的升级换代,公司新产品的研发周期由原来的8个月缩短到了5个月;复产周期由原来的50天缩短到了35天,总体生产效率提高了31%。通过信息化能效检测系统的铺设,使公司对能源的利用率提高了12%,实现全年生产零事故。
绿色发展是高质量发展的底色,新质生产力就是绿色生产力。近年来,兰州电机依托新区优越的发展环境,深入贯彻落实工业节能、资源综合利用、清洁生产、绿色制造等新发展理念,积极开发绿色产品、推行绿色设计,绿色工厂及绿色制造体系建设取得新成效,为企业高质量发展注入更多韧性。
在兰州电机厂区,厂房屋顶上的光伏组件在阳光下熠熠生辉。2017年,兰州电机出城入园整体搬迁的前期,为积极响应国家、省市号召,在兰州新区厂房建设中,设计制造了这个屋顶光伏可再生能源建筑一体化应用示范工程。赵庆礼介绍,该示范工程充分利用主厂房和配套厂房屋顶,沿着厂房屋面平铺安装了总计71278块单晶硅285Wp光伏组件,“这个系统设计运行期为25年,年均发电量约1994.16万千瓦时,可减排二氧化碳16672吨,节能减排效果十分显著。”
除此之外,以工信部智能制造新模式应用项目“基于个性化定制的大中型高效智能化电机数字化车间建设”实施为契机,兰州电机新购置和数字化改造各类生产加工设备1600余台套,主要设备数字化率达到86%以上,数字化的工艺设备、检测仪器覆盖研发设计、加工制造、过程检验、成品试验等全过程。
依托国家级绿色工厂平台,兰州电机推进绿色制造体系建设,按照国家对“双碳”工作的战略部署,开展“企业自身实现碳达峰碳中和,新能源电机产品、高效节能电机产品研发,助力用户实现碳达峰碳中和”等方面的研究,通过使用绿色低碳环保材料、低碳化工艺改进、开发绿色产品等,积极介入双碳领域,优化供应商体系,打造绿色供应链。
“时刻保证技术在行业领先,才能在竞争中保持优势。”赵庆礼说,未来,兰州电机将瞄准“高新特尖”方向和领域,以电机业务为基石,向高效节能、小型轻量、绿色智能延伸,不断开辟新赛道、增强新动能,为新质生产力赋能。
兰州日报社全媒体记者 张丹